?
?
?全自動真空上料機是一種依托負壓氣力輸送原理,通過真空泵(或風機)在密閉管道內形成負壓,將粉體、顆粒狀物料從儲料倉高效輸送至目標設備(如混合機、反應釜)的自動化設備。其廣泛應用于制藥、食品、化工、新能源等行業,在提升生產效率、減少粉塵污染的同時,也對設備的可靠性提出了要求。由于物料特性(如黏性、吸濕性)、工況環境(如溫度、濕度)及連續作業需求,真空上料機易出現堵塞、泄漏、壓力異常等故障,直接影響生產連續性和產品質量。因此,開展故障診斷與維護管理研究,對保障設備穩定運行、降低運維成本具有重要意義。
??一、全自動真空上料機的常見故障類型及機理分析??
??1. 堵塞故障??
??故障現象??:物料輸送流量顯著下降或中斷,真空度波動增大,管道局部出現壓力異常升高。
??發生機理??:
??物料特性影響??:高黏性物料(如濕法混合的中藥浸膏)、易吸濕結塊物料(如淀粉、乳糖)在輸送過程中易附著于管道內壁或彎頭處,逐漸堆積形成堵塞;
??工藝參數失配??:進料速度超過輸送能力(如螺旋給料機轉速過高)、真空度不足(如過濾器堵塞導致抽氣效率下降)或管道傾斜角度過小(物料易在水平段滯留);
??設備結構缺陷??:管道內壁粗糙度過高(如焊縫毛刺未清理)、彎頭曲率半徑過小(物料離心力增大易堆積)。
??2. 泄漏故障??
??故障現象??:系統真空度無法達到設定值(如從-0.09 MPa降至-0.06 MPa),輸送效率顯著降低,噪音異常(如漏氣處產生“嘶嘶”聲)。
??發生機理??:
??密封件老化??:真空管道法蘭連接處的橡膠密封圈長期受負壓拉伸和物料腐蝕(如酸性物料侵蝕),導致彈性下降、裂紋產生;
??焊縫或接頭缺陷??:管道焊接處存在氣孔、未熔合缺陷,或快裝接頭因頻繁拆裝導致密封面磨損;
??機械損傷??:物料中混入硬質雜質(如金屬碎片)劃傷管道內壁,或在搬運過程中碰撞導致管道變形。
??3. 壓力異常故障??
??故障現象??:真空泵運行電流波動增大,系統壓力不穩定(如周期性振蕩),輸送流量忽高忽低。
??發生機理??:
??過濾器堵塞??:物料微粒(如≤50 μm的細粉)在旋風分離器或布袋過濾器表面累積,導致排氣阻力增大,真空泵抽氣效率下降;
??真空泵故障??:葉輪磨損(如葉片間隙增大)、軸承潤滑不良(如油脂干涸)或電機過載(如電壓不穩),導致抽氣能力下降;
??管路設計問題??:主管道直徑過小(如
??4. 電氣控制故障??
??故障現象??:設備無法啟動、自動停機或報警頻繁(如“真空度超限”“電機過熱”),PLC(可編程邏輯控制器)顯示異常代碼。
??發生機理??:
??傳感器失效??:真空壓力傳感器膜片老化(如長期受負壓疲勞)、溫度傳感器探頭污染(如物料粉塵覆蓋),導致信號漂移或失真;
??PLC程序邏輯錯誤??:控制程序未考慮物料特性變化(如黏性物料輸送時未延長進料間隔),或通信協議沖突(如與上位機數據交互異常);
?
?電氣元件老化??:接觸器觸點氧化(如頻繁通斷導致電弧燒蝕)、繼電器線圈絕緣下降,引發接觸不良或短路。
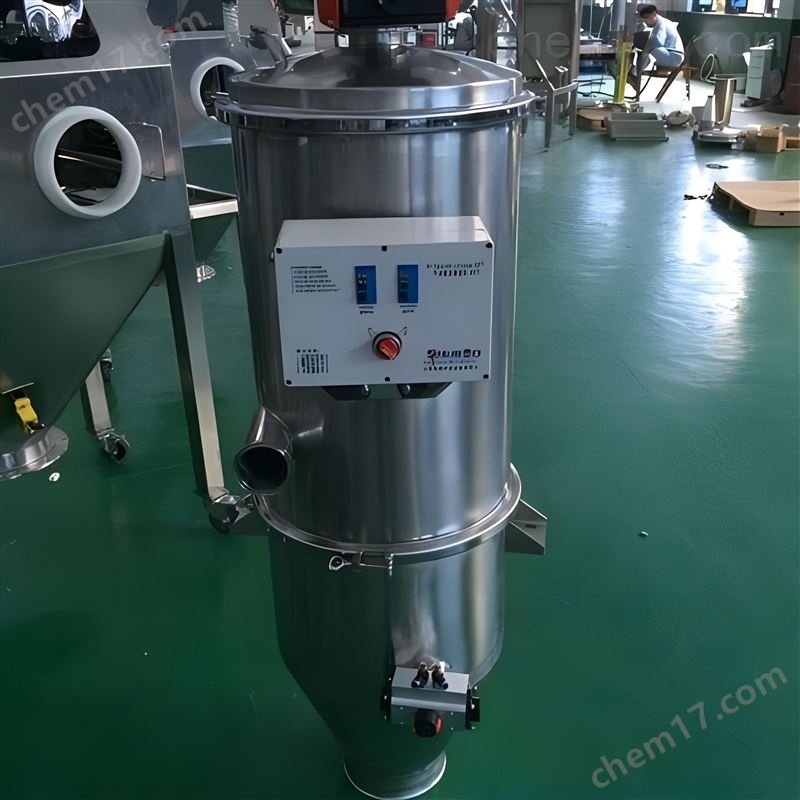
??二、故障診斷技術與方法研究??
針對上述故障類型,需構建“傳感器監測+智能算法+專家經驗”融合的故障診斷體系,實現從“被動維修”到“預測性維護”的轉變。
??1. 基于多傳感器的數據采集系統??
在關鍵部件(如真空泵、過濾器、管道彎頭)布置高精度傳感器,實時采集設備運行狀態參數:
??壓力傳感器??:監測管道真空度(量程-0.1~0 MPa,精度±0.5% FS)、進料口與出料口壓力差(判斷堵塞位置);
??流量傳感器??:測量物料輸送流量(如科氏力質量流量計,精度±0.2%);
??溫度傳感器??:監測電機繞組溫度(防止過熱)、過濾器表面溫度(判斷是否存在物料堆積發熱);
??振動傳感器??:檢測真空泵軸承振動(頻率范圍10~1000 Hz,靈敏度≥50 mV/g),識別葉輪不平衡或軸承磨損;
??電流/電壓傳感器??:采集電機運行電流(判斷負載是否超限)、電源電壓穩定性(防止欠壓/過壓損壞)。
??2. 故障診斷算法與模型??
結合實時數據與歷史故障案例,采用以下算法實現故障類型識別與定位:
??閾值報警法??:對關鍵參數設定安全閾值(如真空度<-0.07 MPa觸發“壓力異常”報警),適用于簡單故障(如過濾器堵塞);
??時序數據分析法??:基于滑動窗口計算參數變化率(如流量突降>30%持續10 s),識別堵塞或泄漏的早期征兆;
??機器學習模型??:
??決策樹模型??:通過訓練歷史故障數據(如“真空度下降+流量波動→過濾器堵塞”),建立故障特征與類型的映射關系;
??神經網絡模型??:采用LSTM(長短期記憶網絡)分析多參數時間序列數據(如壓力、流量的連續波動),識別復雜故障模式(如葉輪磨損導致的壓力振蕩)。
??3. 故障定位與可視化診斷平臺??
開發基于HMI(人機界面)或工業物聯網(IIoT)的可視化診斷系統,集成以下功能:
??故障報警分級??:根據嚴重程度分為三級(Ⅰ級:立即停機,如電機過熱;Ⅱ級:如流量波動;Ⅲ級:觀察隨訪,如輕微壓力波動);
??故障定位地圖??:在設備三維模型中標注故障位置(如“彎頭處堵塞”),并關聯維修手冊中的拆裝步驟;
??歷史數據追溯??:存儲故障發生前后的參數曲線(如堵塞的流量下降趨勢),輔助分析根本原因。
??三、維護管理策略與優化措施??
??1. 預防性維護計劃??
基于設備運行周期與故障規律,制定分級維護策略:
??日常維護??(每班次):檢查密封件是否完好、管道連接是否松動、過濾器表面是否有明顯積料;
??定期維護??(每月/季度):更換磨損密封圈、清理過濾器(采用超聲波清洗避免纖維損傷)、校準傳感器精度;
??專項維護??(每年):拆解真空泵檢查葉輪磨損情況、測試電機絕緣性能、評估管道內壁腐蝕程度。
??2. 智能運維平臺的應用??
構建基于云計算的遠程運維系統,實現以下功能:
??實時監控??:通過4G/5G網絡傳輸設備狀態數據至云端,支持多終端(手機APP、PC端)查看;
??預測性分析??:利用機器學習模型預測關鍵部件(如真空泵軸承)的剩余壽命(RUL),提前安排備件采購與停機檢修;
??專家遠程診斷??:當本地系統無法定位故障時,上傳實時數據至云端專家庫,由專業工程師遠程分析并指導維修。
??3. 備件管理與成本控制??
建立數字化備件庫存管理系統,優化備件存儲與采購策略:
??關鍵備件清單??:根據故障頻率與停機損失確定優先級(如真空泵葉輪、PLC主板為A類備件,需常備庫存);
??供應商協同??:與核心部件供應商簽訂“快速響應協議”,縮短備件交付周期(如48小時內到貨);
??成本效益分析??:對比維修成本(如更換密封圈的人工+材料費)與更換整機成本,制定經濟性維護決策。
??四、案例分析:某制藥企業真空上料機故障診斷實踐??
??1. 故障背景??
某制藥企業的全自動真空上料機在輸送中藥浸膏(黏度>5000 mPa·s)時,頻繁出現“流量波動+真空度下降”報警,日均停機時間達2小時,嚴重影響生產進度。
??2. 診斷過程??
??數據采集??:通過多傳感器系統獲取以下數據:
真空度從-0.09 MPa波動至-0.06 MPa,波動周期約15 s;
流量從設計值150 kg/h降至80~120 kg/h,突降現象與真空度波動同步;
管道彎頭處壓力差異常升高(從0.02 MPa增至0.05 MPa)。
??故障定位??:結合時序數據分析與機器學習模型,判定為“彎頭處物料黏附堵塞”,與高黏性物料特性及管道曲率半徑過小(R=2D,D為管道直徑)直接相關。
??3. 維護措施??
??短期處理??:停機后采用高壓空氣反吹彎頭(壓力0.6 MPa),清除積料;
??長期改進??:更換為大曲率半徑彎頭(R=5D)、在進料口增設預加熱裝置(降低物料黏度)、優化進料速度控制邏輯(根據真空度動態調整螺旋給料機轉速)。
??效果驗證??:改造后故障頻率從日均3次降至每月1次,輸送效率提升至設計值的95%以上。
??五、結論與展望??
全自動真空上料機的故障診斷與維護管理需以“數據驅動”為核心,通過多傳感器監測、智能算法分析與預防性維護策略的協同,實現從“被動響應”到“主動預防”的轉變。未來發展方向包括:
??數字孿生技術??:構建虛擬設備模型,實時映射物理設備的運行狀態,提前模擬故障場景并優化維護方案;
??邊緣計算應用??:在設備端部署輕量化AI模型(如TinyML),實現故障診斷的本地化快速響應,減少云端依賴;
??全生命周期管理??:整合設備采購、安裝、運行、報廢數據,建立“一機一檔”電子檔案,為運維決策提供全景支持。
通過技術創新與管理優化,可顯著提升真空上料機的可靠性與經濟性,為制藥、食品等行業的高效生產提供堅實保障。